Plastic has quickly become one of the go-to materials in furniture making due to its versatile nature and wide array of design possibilities. Plastic's primary advantages are that it is both relatively affordable and easily replicated - making it cost-effective when producing large volumes. Plastic can also withstand wear and tear more readily than other materials - however strict quality control must still be implemented during production to prevent defects from emerging that compromise the integrity or load-bearing capabilities of its furniture.
Selecting the proper plastic chair mold for your business is crucial to producing high-quality products. While various processes may be employed such as injection molding, blow molding and rotational molding - each has their own individual advantages but you should select whichever best meets the needs of your operation.
Injection molding is an efficient and accurate way to produce plastic chairs, offering the greatest accuracy and precision. The process involves injecting hot molten plastic into a cold mold before it solidifies - this method can produce plastic chairs of various shapes and sizes and works great when producing large quantities at once.
Another popular method for producing plastic stools is through blow molding. Similar to injection molding, blow molding uses air pressure instead of liquid to mold plastic into desired forms and designs. This technique can create hollow designs while providing complex forms that would be impossible with injection molding alone.
Rotational molds provide uniform wall thicknesses and make an economical option for short-run productions, with less expensive tooling and faster production than injection molding. Rotational molding offers businesses who require small quantities quickly an affordable way of producing plastic stools quickly.
Before buying a plastic stool mould, it's important to carefully consider your product size and intended use. For example, if you plan to produce large quantities of stools at once then opt for a larger mold; this will save time and money during production as it will make it easier to remove molded pieces after the formation stage. In addition, ensure your mould's cooling system can handle its required temperature range - you don't want any warping or melting during manufacturing!
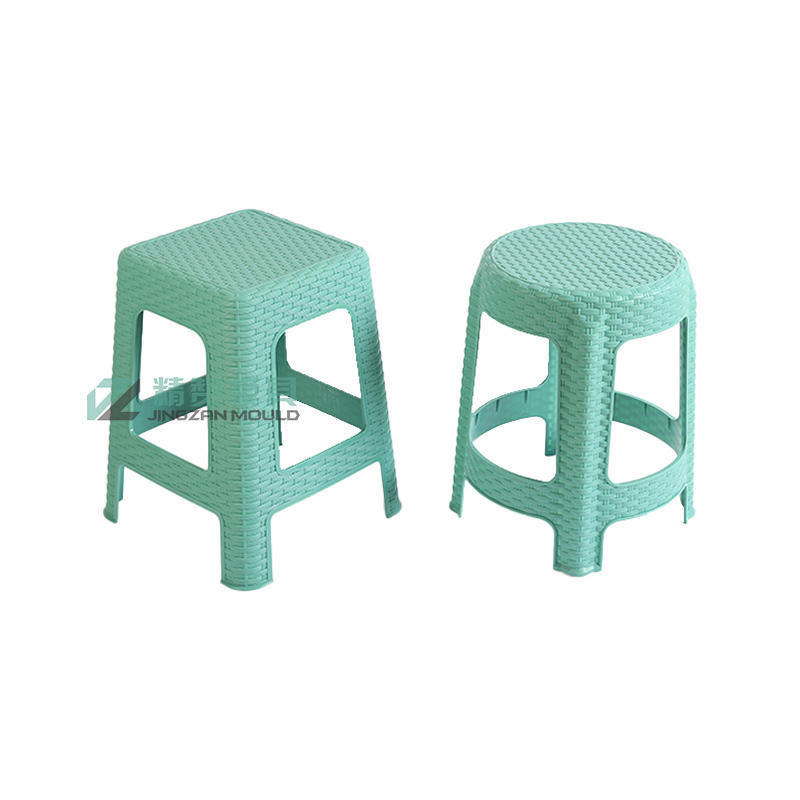